
Vapor phase oven use the vapor layer that transfers the latent heat when it condenses, in contrast to HACR, which utilizes hot air for transferring heat into the PCB as well as its components since it moves through a system present on the conveyor belt.
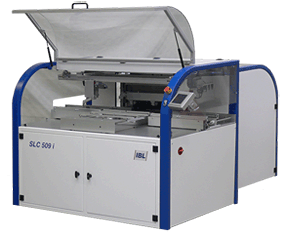
A second problem is that if a limited run is involved, the buyer might not be ready to deliver the necessary test PCB assembly. The first disadvantage is that it takes time to complete the task because a specific temperature profile is required for uniformly proper soldering. Thermocouples are used on the test circuit assembly to measure the temperature change as it passes the oven during profiling. These elements alter the pace at which heat is transferred from hot air immediately it circulates inside the oven. In addition, the components’ color also affects the profile since darker colors absorb heat faster and readily than lighter or reflective colors. The HACR profile is significantly influenced by the PCB’s thermal mass as well as the components present on it. HACR procedure primarily utilizes hot air, which isn’t always an appropriate method for soldering. To achieve uniform soldering throughout the board when employing the IR reflow method to solder the PCB assembly, a special reflow profile must be created. These developments have made it possible for reflow soldering to produce surface mount devices with soldering of the greatest quality. Second, there has been number of improvements made to ir reflow soldering techniques throughout time. That capability permits the manufacturing of the circuit boards in a large volume very quickly. The oven technique, in particular, has a far higher soldering capability than the hand soldering. These electrical components are now permanently attached to the pcb board because the solder has set.įor a few reasons, reflow soldering can be frequently used in the manufacture of circuit boards. Each circuit board passes through a cooling cycle after its oven stage. This solder paste melts as a result (reflow). The PCB goes through the oven while being reflow soldered. Electrical components must stick to the board as a result of this. The solder paste, made of solder flux and solder, is applied to the essential parts of the circuit board during the procedure. Soldering Using IR ReflowĪ typical technique for the quick manufacturing of PCBs is IR reflow soldering. Here, we contrast the two soldering techniques.

Vapor Phase Reflow was discovered in our quest to increase the efficiency of the surface mount assembly process, and investing in these devices and systems has successfully eliminated delays. The IR reflow, which has to do with the profiling of each Circuit board type and took a significant period of time, was included among the assembly line’s bottlenecks. Our company has been constantly searching for cutting-edge technology that can speed up assembly while enhancing PCB quality.
